The project team in Marysville Auto Plant Weld set out to destroy oxidation’s effects…and they succeeded.
Rust spots on a vehicle are reminders that Father Time and Mother Nature always win. However, a recent project team at the Marysville Auto Plant (MAP) was successful in beating them, for at least a few more years.
In 2018, MAP Weld Department associates identified an opportunity to improve corrosion resistance for Honda and Acura vehicles built at the plant, further fulfilling—and exceeding—customer expectations.
Countermeasuring
Honda associates pride themselves on producing durable products, with durability that goes beyond the vehicle powertrain or electrical components and includes all aspects of the vehicle, including appearance. A team of MAP associates in the Weld Department knew there was room for improvement, so they formed a project team to improve vehicle durability.
The team’s primary concern area was hem flanges. A hem flange is where two pieces of metal are joined together.
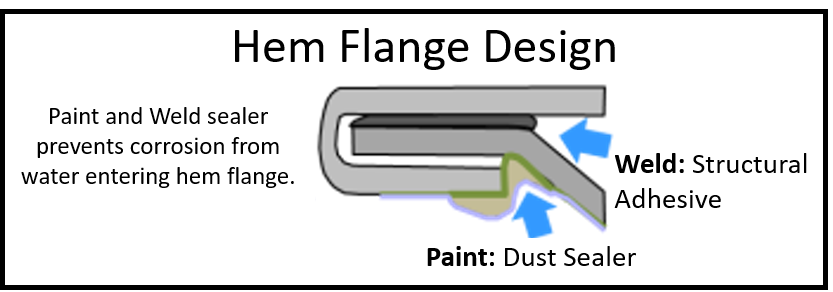
Within the Weld Department, a structural adhesive is used to prevent water from entering the hem flange and prevents corrosion.
“I discovered that MAP’s sealer application had room for improvement,” said Scott Webb, who was assigned as MAP’s corrosion resistance lead for the Weld Department. “If the hem sealer isn’t applied to exact specs, water can enter the joint and the unpainted metal is exposed. That’s why a team of associates began to attack sealer application accuracy and volume control to better meet the vehicle specification.”
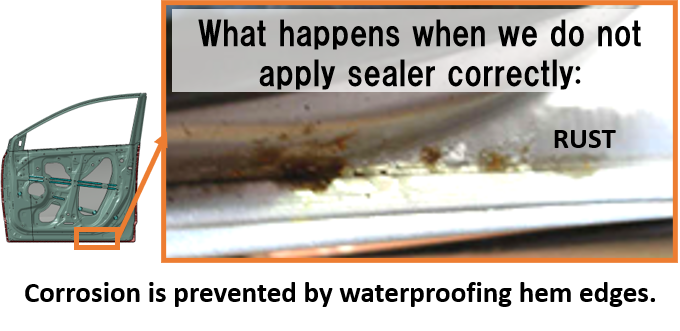
Upon further investigation, the team identified multiple root causes:
- The optimal sealer location was not known;
- The current application system wasn’t meeting requirements on 100% of production; and
- The inspection requirements were not defined.
Any one of the root causes could lead to future corrosion. So, the team had to countermeasure each of the issues in order to eliminate water intrusion into the hem seal.
Finding the right spot
The first—and most important—step was to identify the optimal sealer location based on the vehicle design drawings. Once the team identified that location, they updated the robot-teaching procedure into ISOQuest, Honda’s quality procedure system.
With the sealer location identified, the team developed a template to install on the equipment.
“I developed a template to transfer the optimal sealer location from the frame to the skin,” Webb said. “This method greatly reduces maturation time and scrap. Since the process is likely to benefit Weld Departments at other plants, it is being considered as an official procedure.”
Hitting 100
In addition, a new sealer application system replaced the old air-compressed system. The result is consistent application to the ideal location on every part produced.
“The new equipment upgrades, application techniques, and check methods have greatly enhanced the corrosion resistance of vehicles built here,” Webb said. “We succeeded in improving MAP’s ability to produce corrosion resistant hem flange enclosures.”
Requirements defined
The last concern area to resolve was to incorporate a confirmation system that could meet defined inspection requirements. This step required innovation not used anywhere within Honda.
“An overlay vision system was developed to provide an easy visual quality confirmation of the application location for our associates,” said Taylor Jones, a MAP Weld engineer and overlay project leader.
A security camera placed above the sealer application equipment sends a live feed to a 70-inch screen located above the loading station. The overlay shows the exact application area per the vehicle specifications.
Inspection is now a quick glance to see if sealer is within the desired locations.
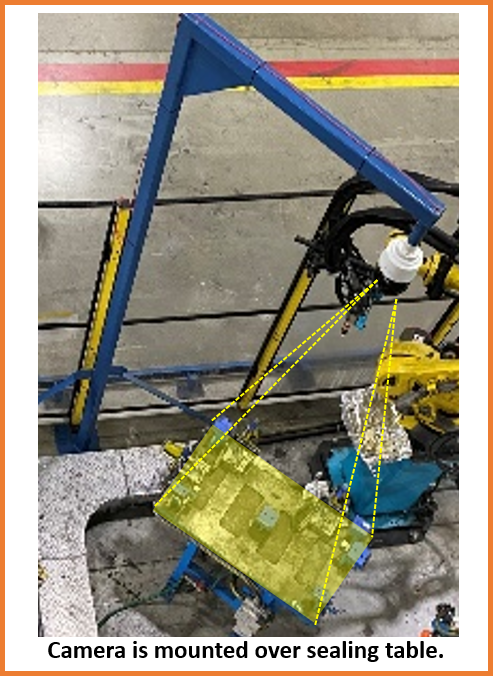
“The virtual template shows the associate if the sealer is in the right location,” Jones said. “Once confirmed, the associate presses a button and the image for that part is saved in a database.
“As technology improves, sealer is becoming more important to the integrity of the cars that we design and build. This project gives Honda the opportunity to make sure that the quality of our sealer is the best that it can be.”
Awarded and onward
The team received a silver award in the 2021 Best Quality (BQ) Awards for their work to improve vehicle quality. Other BQ team members include MAP associates Nick Latiano, Mitch Current, Wendell Ellison, and Austin Pence.
The team’s success will certainly delay the impact of Father Time and Mother Nature on Honda and Acura vehicles. MAP is expected to incorporate the project team’s application and confirmation system for all hem weld equipment locations by the end of 2022.
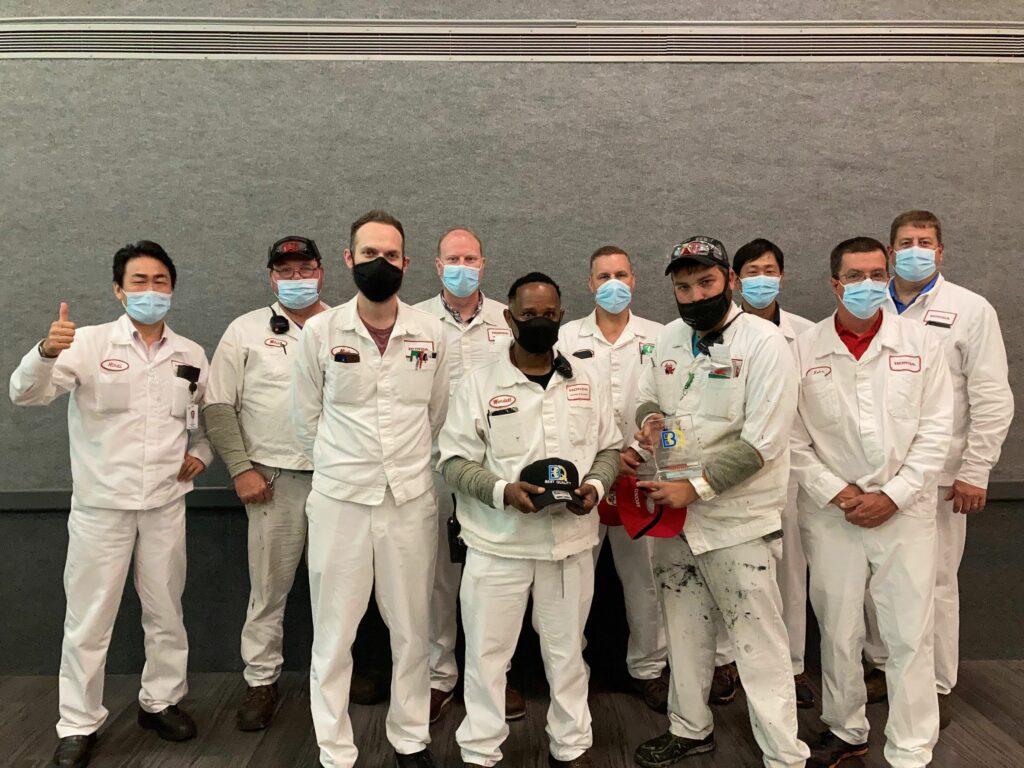
Though this selection process was specific for MAP, other HDMA locations and business units hold their own versions of this activity.