The Alabama Auto Plant’s (AAP) engine plant confronted a new challenge for the 2023 Honda Pilot: manufacturing a completely new engine for the first time since the plant opened.
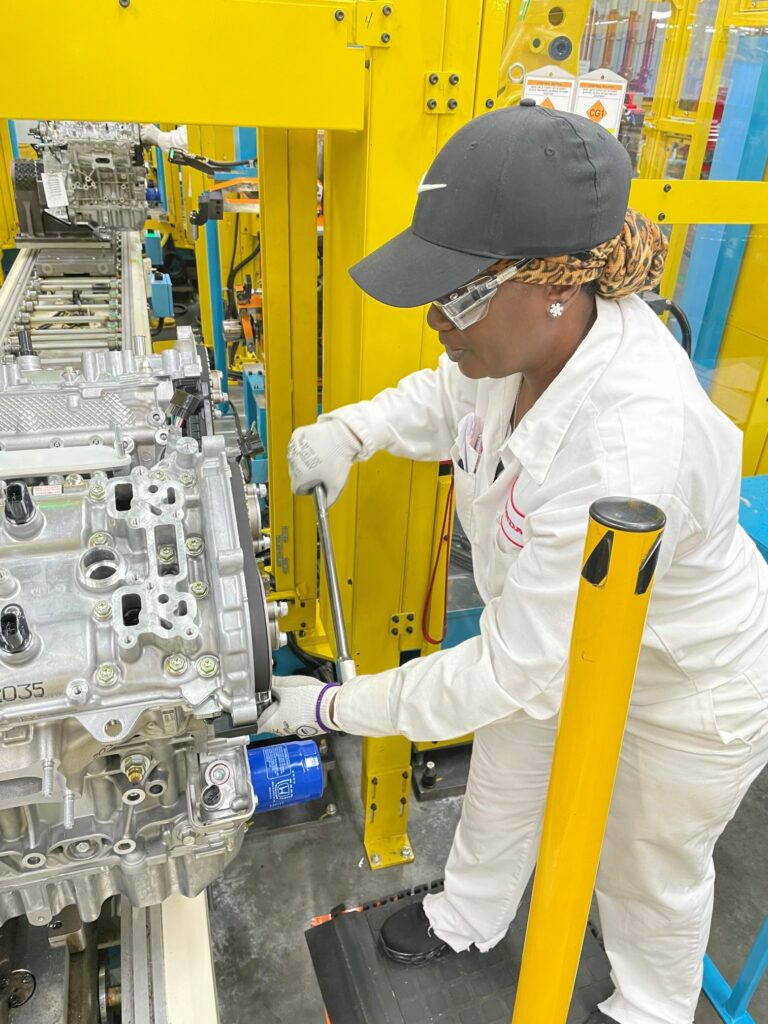
But thanks to hard work and collaboration, AAP is manufacturing an engine fitting the excellence of the new Pilot. AAP worked with associates from the Anna Engine Plant (AEP) and Auto Development Center (ADC) in Ohio, Japan (4-MOC) and other locations to bring production of the new engine on board and at a greater capacity.
The project started over six years ago, said Brett Price, large project leader (LPL) of the new Pilot engine, in charge of the big picture of production of the new engine. He made sure AAP connected with other associates in the company to utilize expertise within Honda.
“Since this was AAP Engine Division’s first full model change, our biggest challenge was that we just didn’t have the resources, systems or flows established locally to handle this level of change,” Price said. “AAP has launched many new models on the frame side, so their process is well established, but for this engine, we had to rely heavily on Anna’s guidance and expertise.”
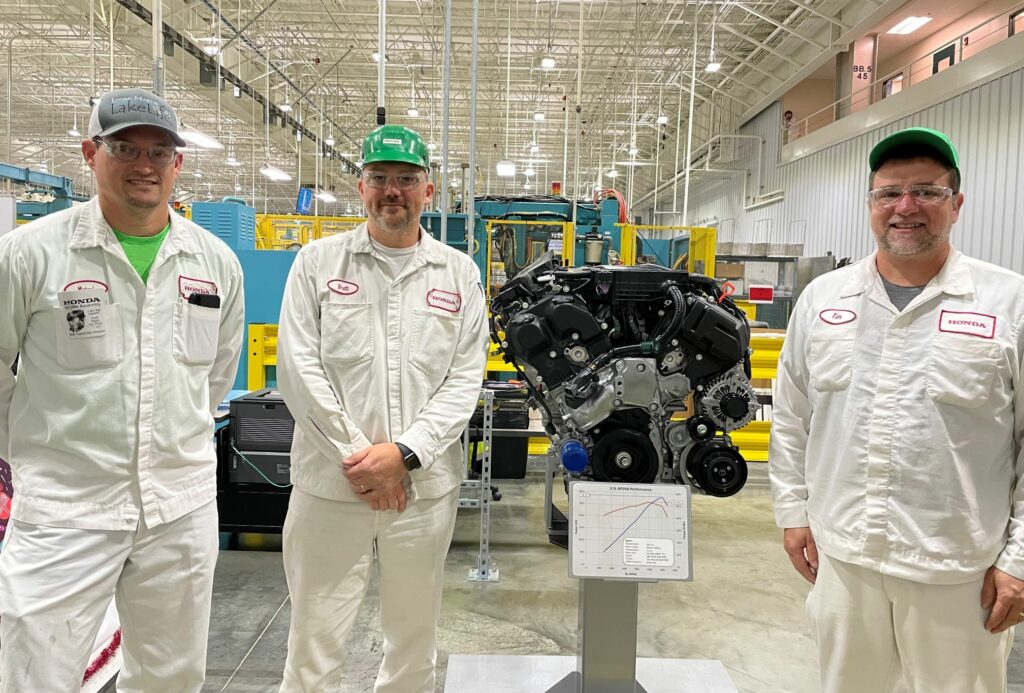
According to New Model Engineering Project lead Tim Pohlman, the Pilot requires production of over 600 engines per day on the AAP Engine Assembly Line.
“There has been a lot of teamwork from the very beginning,” Pohlman said. “At Anna, we produce so many types of engines, including the Type R, NSX and Type S engines. AEP has a lot of experience doing full model changes. Alabama, on the other hand, has built the same V6 light truck engine since 2001 with very little change. We knew there would be gaps where they would need support, and we were ready to step in to help.”
Mike Brush, project lead at AAP for the Pilot engine assembly, said the new engine brought challenges not yet seen at AAP.
“Typically, a new engine model for us would involve a handful of parts or wiring harness changes,” he said. “It has been little things in the past. With the new Pilot engine, there are 101 additional parts versus our current V6 that we’ve been building for over 20 years. In addition to the additional parts, there also is a new level of component complexity that we had to adapt our equipment and processes to.”
“The Pilot engine is unquestionably different from its predecessor, especially the upper part of the engine where the DOHC integrated cylinder head structure exists,” Pohlman agreed. “AEP added new casting, machining, and valve assemble lines to produce the front and rear cylinder head, and these are the most challenging heads ever produced at AEP.”
The team at AAP also rose to the challenge.
“Our goal was to get this engine online as quickly as possible for trial builds because we knew that the quicker our team could get their hands on it, the better our chance of success would be,” Price said. “We’ve been running small weekly training builds on our mass pro line since March 2021. That provided valuable opportunities to train and debug our processes, new equipment, ergonomics, and tools and get those items checked off our list early on. As we moved into the larger trial lots, we were able to focus on the hot spots and top concern areas more deeply to ensure we can delivery a truly exceptional product!”
And the proof of that hard work is in the Pilot driving experience.
“During one of my recent visits to AAP, I had a chance to drive the all-new Pilot,” Pohlman said. “With the new valve-structure system, it’s a much quieter engine. Also, the 10AT (transmission) makes the drive experience smooth. I’m excited about it.”
There were other benefits of the work. “To me,” Price said, “this was a great example of our team, not just here locally in Alabama, but as a region being able to come together and deliver a great new product for our customers. We were out of our comfort zone from the beginning, but everyone gave it 100% effort to ensure success. The Anna team was there to support us when we had questions and when we got stuck. It is a great example of the one team Honda.
“Our folks matured a lot at every level, from engineers to process associates. The thing I take away the most is that we’re all much, much stronger as a group having gone through this.”
“The teamwork between Anna and Alabama associates has been exceptional,” Pohlman said. “It has been very satisfying for me to see two plants 600 miles apart work together like they’re just down the street.”
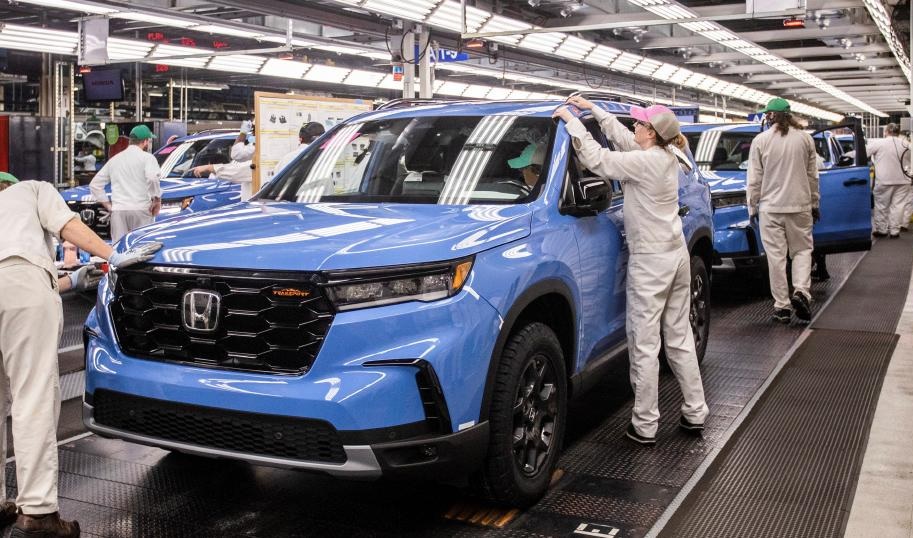
And Brush said there’s more to celebrate. “I’m proud of the fact that our team was able to modify nearly every machine on our floor, rearrange two areas of our conveyor system and incorporate all of the new processes within a reasonable level of investment. In the end, we were able to achieve the budget forecast that we set nearly four years ago.”
Despite all the challenges – which included the COVID-19 pandemic, supply issues and the reorganization of Honda Development & Manufacturing of America – the team succeeded. And they should take pride in their accomplishments, Pohlman said.
“Through this project, we were dealt a lot of different challenges,” he said. “Thanks to the associates for their flexibility and determination. Delivering a brand-new engine platform into mass production is trying by itself, but when you have challenges hitting you that are out of your control it’s more difficult. Both teams at Anna and Alabama did a great job keeping the task at hand to successfully launch this engine into mass production. I can’t wait to see the new Pilot do well in the market.”