Here’s a look at how the MDX has traveled from Canada to Alabama to Ohio, overcoming challenges and hurdles thanks to Honda Development & Manufacturing of America associates.
Building precision crafted performance is no easy task. It takes a fine mixture of challenging spirit and passion, mixed with dreams and joy—and there’s no doubt that our associates have exceeded expectations.
Since it started mass production in 2000, the Acura MDX has been built at three different North American locations, spanning 1,609 miles and two countries. In January 2021, the full model change Acura MDX was released as the new flagship for the Acura lineup. Then the first MDX to wear the Type S badge rolled off the line in December at the East Liberty Auto Plant in Ohio.
Revving up
The story of the MDX’s production began more than 20 years ago in Alliston, Ontario as Honda of Canada Manufacturing (HCM) Line 2 produced the first version. This was the first time HCM Line 2 had launched a brand-new vehicle on their own, as part of the North American team.
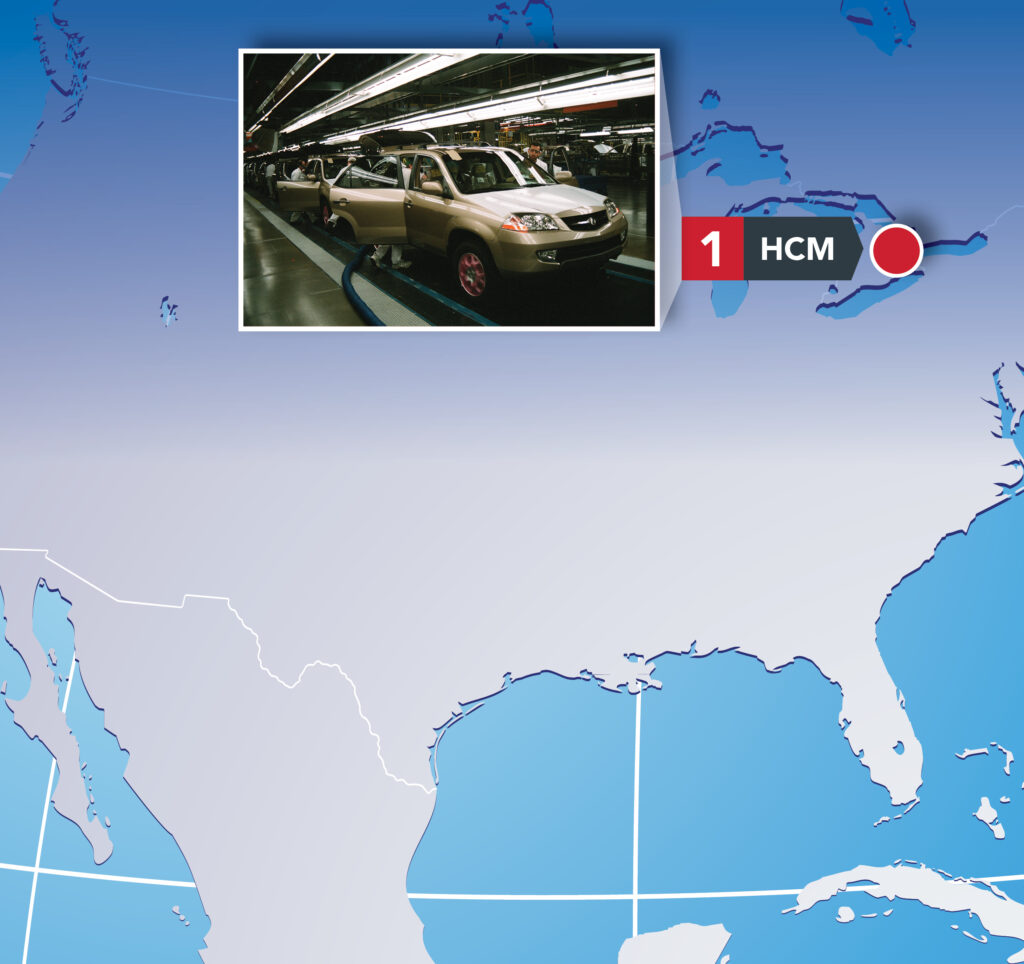
“The team in Canada was very excited and proud that they were going to be making the first Acura SUV,” said Kevin Faubert, Assembly Frame (AF) Department Manager and AF Line Quality Team leader. “The first word that comes to mind is pride. There was so much pride in being chosen as the plant to build the very first Acura SUV. There were many challenges to be met.”
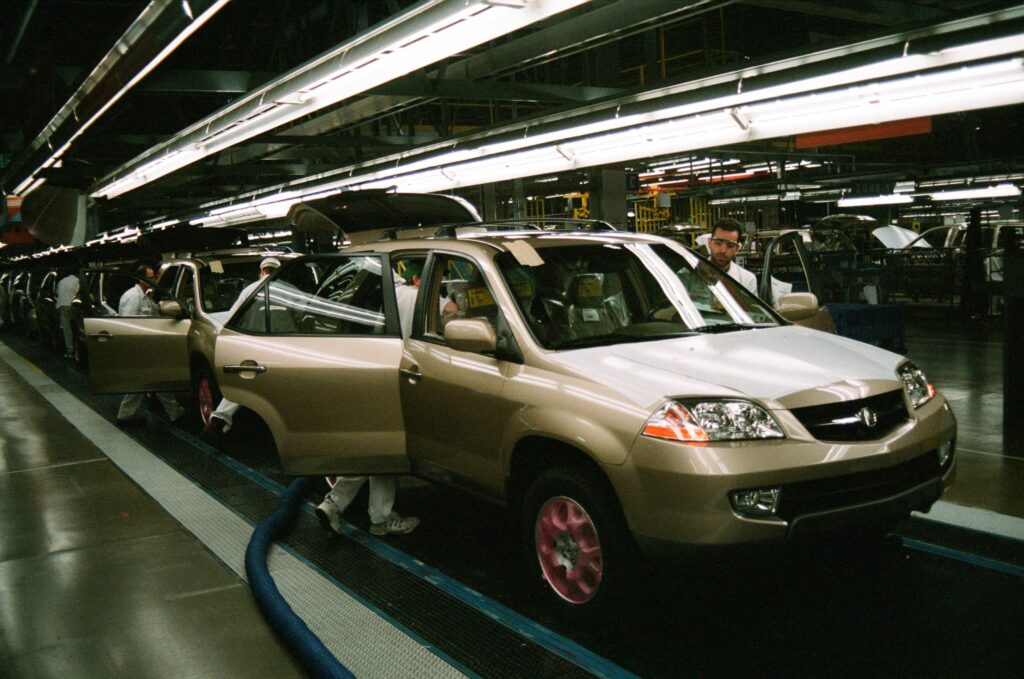
No stranger to challenges, HCM Line 2 started production in 1998 with Honda’s hot-selling Odyssey. “One of the biggest challenges was that we were still ramping up the Odyssey to full capacity and at the same time we were doing our MDX test builds,” recalled Alan Branson, New Model Project Manager for the original MDX and current Group Leader New Model Department.
The MDX was Acura’s first foray into the unibody SUV market, built on Honda’s global mid-size platform. There were many processes for the team to review, adapt, and change to fit the new vehicle.
“Acura brand requirements have tighter specs, fit and finish, and color match. We had to step up our game when it came to producing this SUV,” said Faubert.
But the team at HCM was up for the challenge.
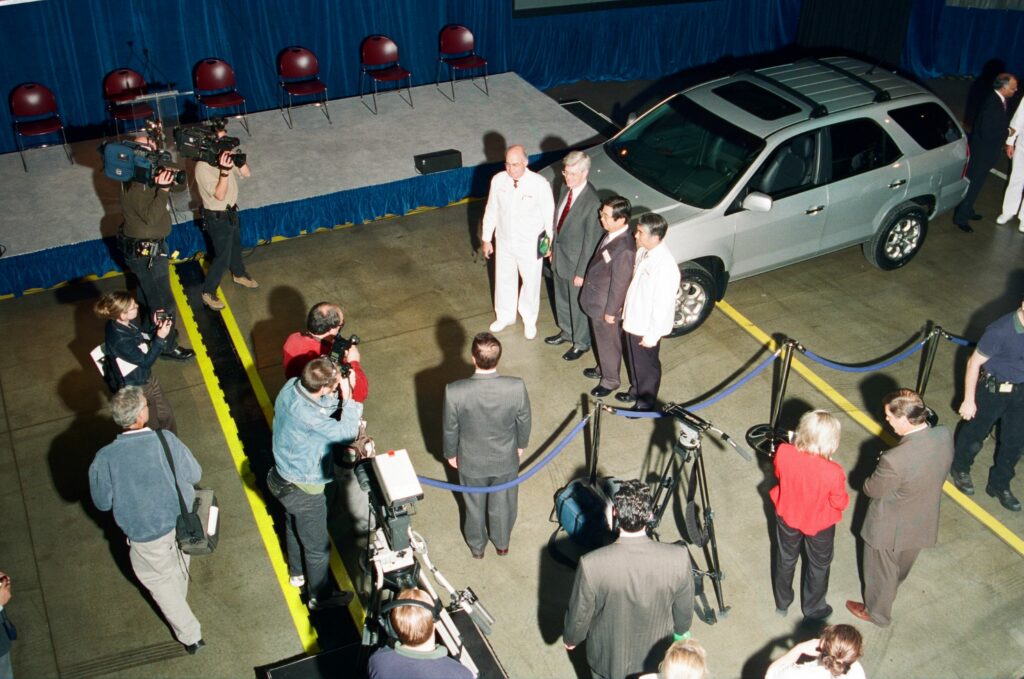
Branson remembered, “The analysis teams had to troubleshoot multi-departmental issues and implement permanent countermeasures across departments, whether by design or manufacturing improvements. As much as possible, we strived for Acura level quality for all models across the board.”
The MDX quickly became a consumer favorite. “We knew the vehicle was getting great reviews,” Faubert said, and pride was felt at every level in the plant.
Among the positive reviews included the distinction of being named 2001 Motor Trend SUV of the Year.
After producing two generations of MDX, the third generation MDX production traveled south to the Alabama Auto Plant (AAP), where a group of Honda associates overcame a different set of challenges.
Less weight, better fuel efficiency
Planning for the move to AAP began in 2009, and there was a lot of preparation required to get the plant ready. The Alabama plant had never manufactured an Acura vehicle, and this new version of the MDX included a new platform and new technologies that required additional thought processes and planning.
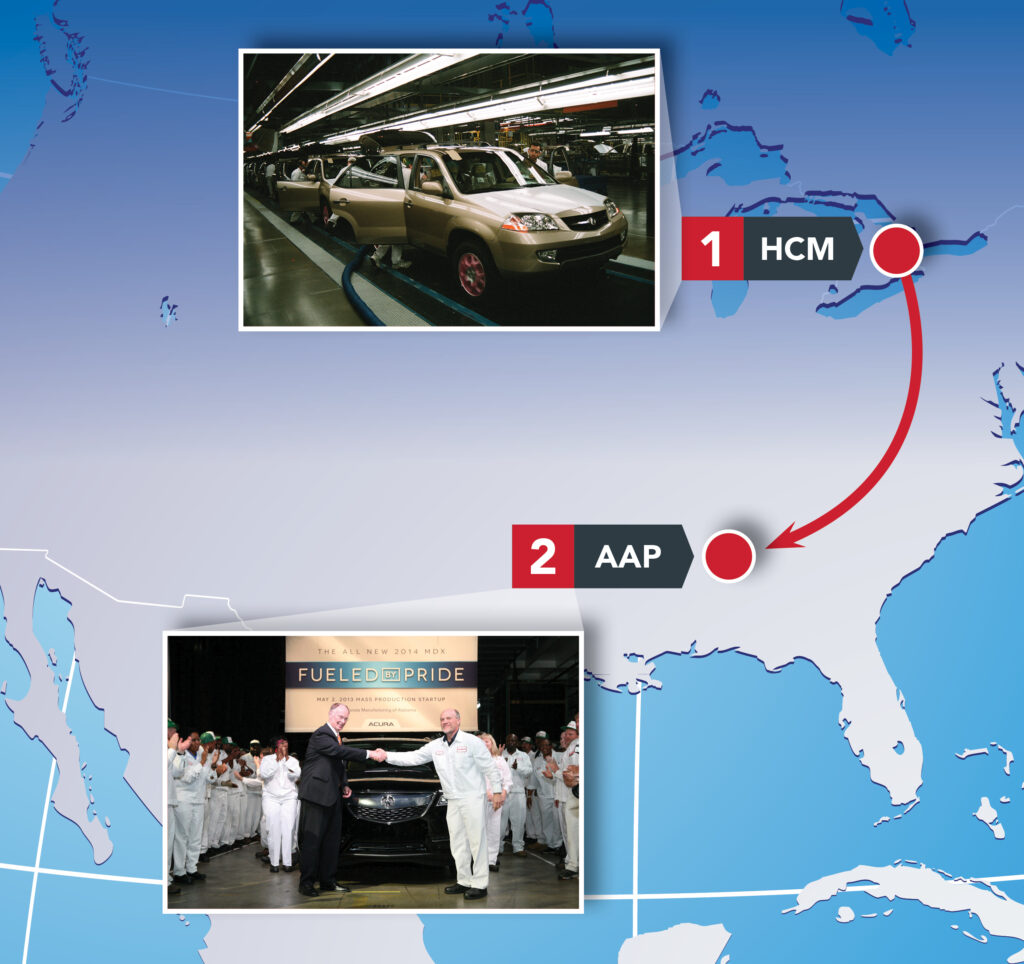
“When development of the third-generation MDX began, the North American automobile market was still recovering from the Lehman shock and the global economic crisis that drove gas prices to exceed $4 per gallon,” AAP Engineering Project Lead John Deno recalled. “Consumers were in the market for vehicles with high fuel efficiency. In response, the MDX team had to improve aerodynamic performance and make reductions in vehicle weight of nearly 250 pounds (115 kilograms).”
The MDX team at the North American Auto Development Center (ADC) began considering various options to reduce the weight of the vehicle. Among the solutions they applied were a hot-stamped 1500 megapascal, ultra-high-strength-steel door ring, high strength steel in-house floor stampings, an aluminum hood, and aluminum fenders.
The team also applied the new 3.5L Direct Injection V6 engine that had been developed for the recently re-designed Acura RLX. This engine was developed to keep the performance of the outgoing engine, while also enhancing the efficiency of direct fuel injection and variable cylinder management.
“These changes to the body construction and powertrain, along with a multitude of other small incremental improvements, allowed the development team to improve fuel economy by 4 MPG and achieve top in class ratings,” Deno said.
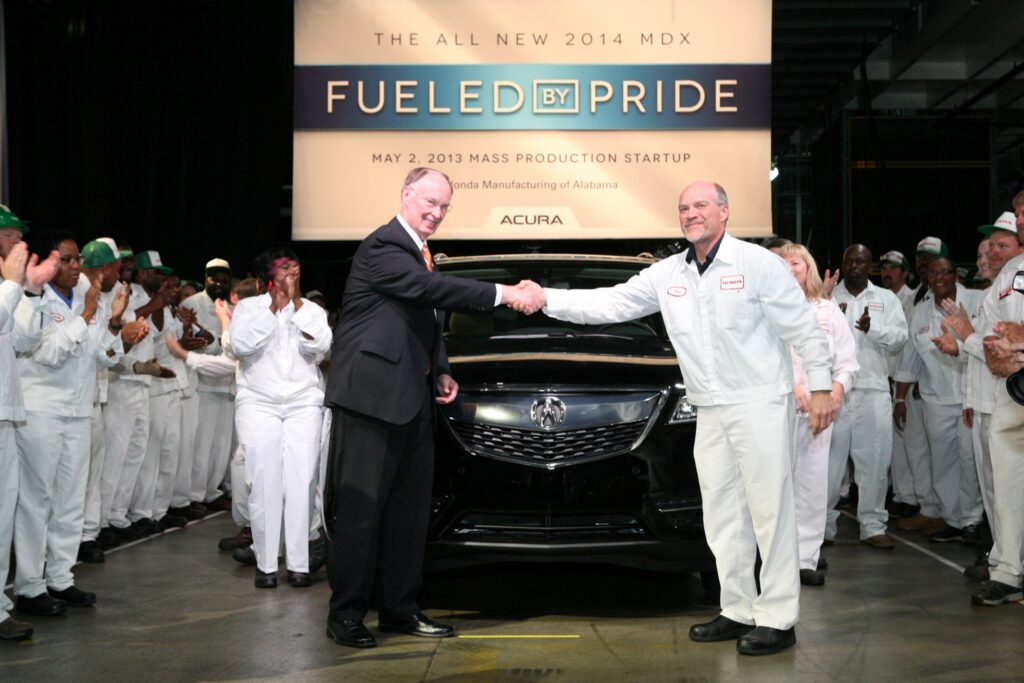
For fit and finish
With the MDX, AAP had its first opportunity to work with R&D engineers from ADC on an Acura vehicle development.
Deno recalled, “We got started in late 2009, and there was a big focus within ADC for the Acura Quality Standards (AQS). They had a set of different quality standards; they wanted to be able to differentiate the Acura from the Honda. One of those areas was in the paint quality.”
The team did not have the time or the budget to completely renovate the paint department, so they looked for a different approach.
“Members from the ADC in Ohio joined forces with AAP and North American paint suppliers to identify the available technologies to achieve the AQS targets. For the first time, terms such as shortwave, longwave, and WA (a measurement of paint finish quality) entered into daily conversations as the team developed their know-how of luxury brand paint appearance,” according to Deno.
The newly formed team began extensive testing and found there were many small changes that finally produced the desired results. The combination of changes included the material applicators, application patterns, robot speed and accuracy, oven temperatures and profiles, and materials formulation.
In May of 2013, the first Acura MDX rolled off the line in Lincoln, using more than 55% lightweight materials and weighing 250 pounds less than the previous version.
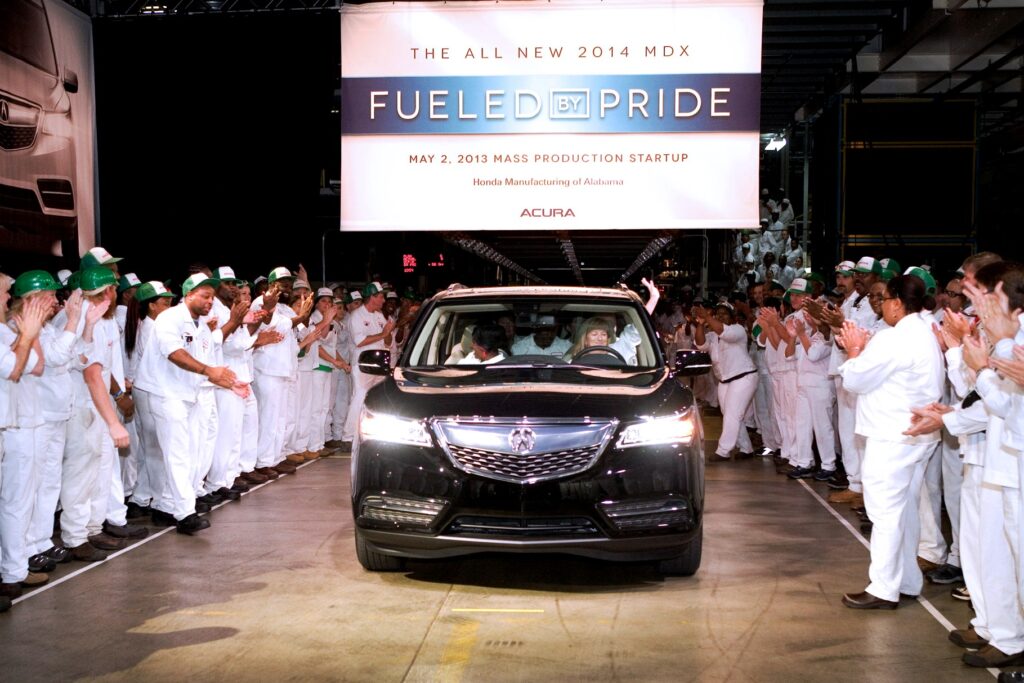
Alabama produced more than 290,000 MDXs in the 53 months between April 2013 and September 2017. But then it was time for MDX to transition yet again: It traveled north, this time to the East Liberty Plant (ELP) in Ohio.
Another move, another success
The MDX move to ELP occurred mid-cycle, adding to what were already large challenges for the ELP team. One of the biggest hurdles was size. ELP was originally designed and built to manufacture Civics, and the MDX was almost 30 inches longer, more than 12 inches wider, and 13.5 inches taller.
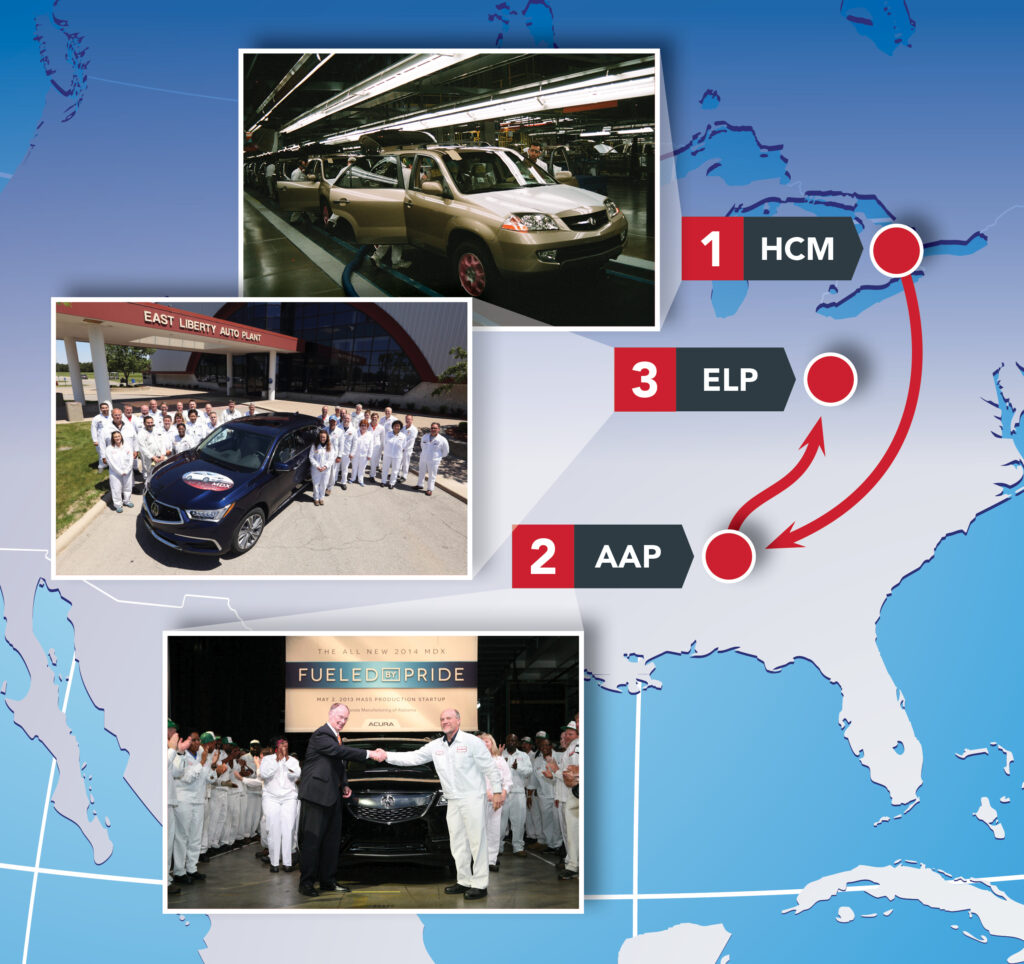
That meant the team would have to adjust and even change the structure of a building.
Jared Ressler, from ELP’s Paint Manufacturing Characteristics and Regional Operations Genpo Engineering, was on the team that had to update the processes and then solve the problem of a bigger vehicle in the same size painting area. They found many areas where the vehicle simply would not fit, and the hangers were a particular challenge.
Ressler and team decided to use a 3D printer to create and assemble an MDX body so they could see how it would move through the dip tanks, paint processes, ovens, inspection, and then to assembly.
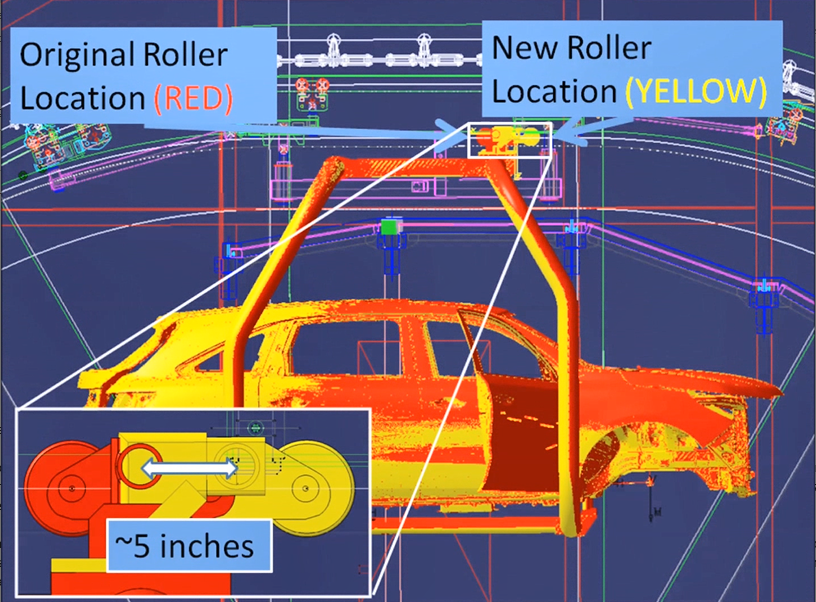
These lessons have become a new standard at ELP. “Through this process, we learned that a kinematic simulation is an excellent tool for understanding the motion of the car throughout the conveyor system and more kinematic models have been created to study other areas,” Ressler shared.
Wrapping Up
The story of the Acura MDX in North America can be summarized as a story of associates rising to the occasion. In two decades, the Acura MDX has traveled 1609 miles (2623 km) to three different North American plants.
Honda associates at HCM, AAP, and ELP demonstrated their challenging spirit to overcome many challenges, innovate, and produce a vehicle that demands the highest level of quality, precision, and performance. They had to invest a significant amount of time in the transfer of the model to and from each plant, and this is the collaborative teamwork that led to the success the MDX has experienced.
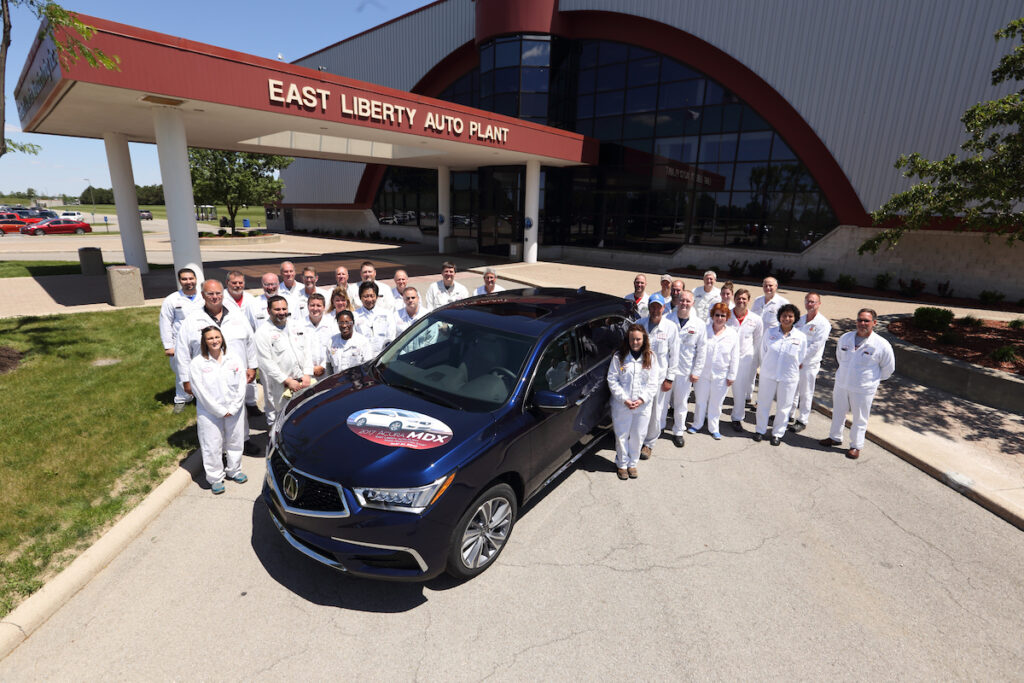
The results of their efforts speak for themselves as MDX sales have exceeded one million vehicles, making it the best-selling three-row luxury SUV of all time. And on December 23, 2021, the first MDX Type S began a new chapter in its history, becoming the first SUV to wear the Type S badge.
All of this has been possible thanks to the passion and challenging spirit of associates, manifested in ingenuity, perseverance, and dedication.