Marysville Auto Plant’s renewed stamping press is ready for the future.
Ka-BOOM! Ka-BOOM!
You hear—and feel—the plant’s stamping presses shape sheet metal into exterior parts used to build the vehicles we produce at Honda.
Each stamp of the press requires pinpoint accuracy and thousands of pounds of pressure applied within a split second. The process is very sensitive, and a dirt particle the thickness of a human hair, or just 40 microns, can cause a surface deformation.
Extended life
“In the past, Honda would replace a stamping press as it approached end-of-life,” said Alex Zats, D-Line renewal project leader at the Marysville Auto Plant (MAP). “Replacement is very costly, and we have three aging press lines: two here at MAP and one up the road at the East Liberty Auto Plant (ELP).”
With the presses aging, a decision had to be made to either replace them or perform a full overhaul to renew each press. A new press has a life expectancy of 30 years or more, while an overhaul adds about 20 more years to the current press’s usefulness.
However, the price tag for an overhaul is less than half of the cost to install a completely new press line.
“Ultimately, the stamping project team decided that the best path forward was to install a new press line at ELP to increase capacity and renew one at MAP,” Zats said.
Once the new press was installed at ELP, MAP associates began renewal of their first press, which came online in November 2021. This approach minimized impact to production by transferring capacity between presses as the first MAP press went offline for renewal.
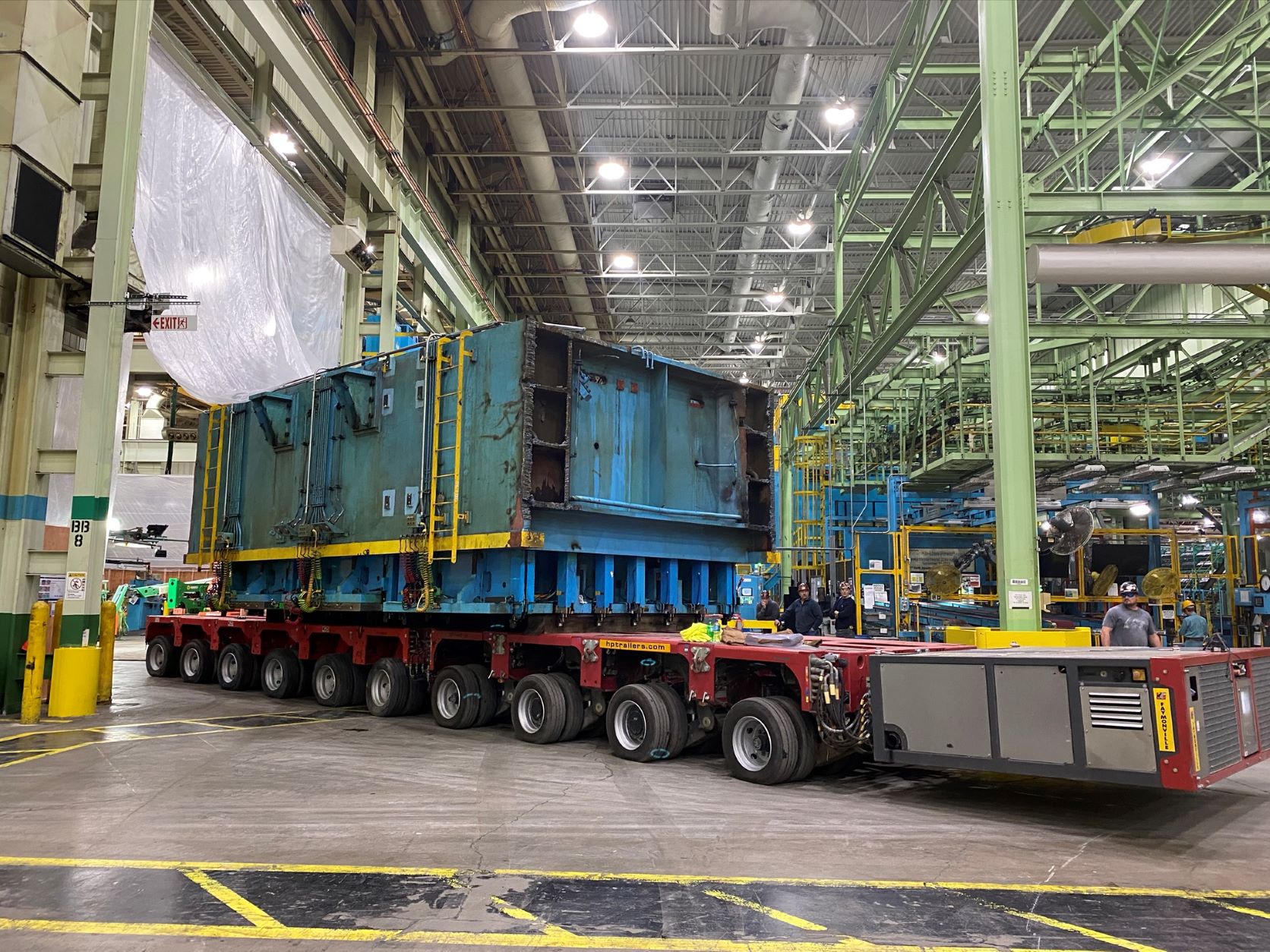
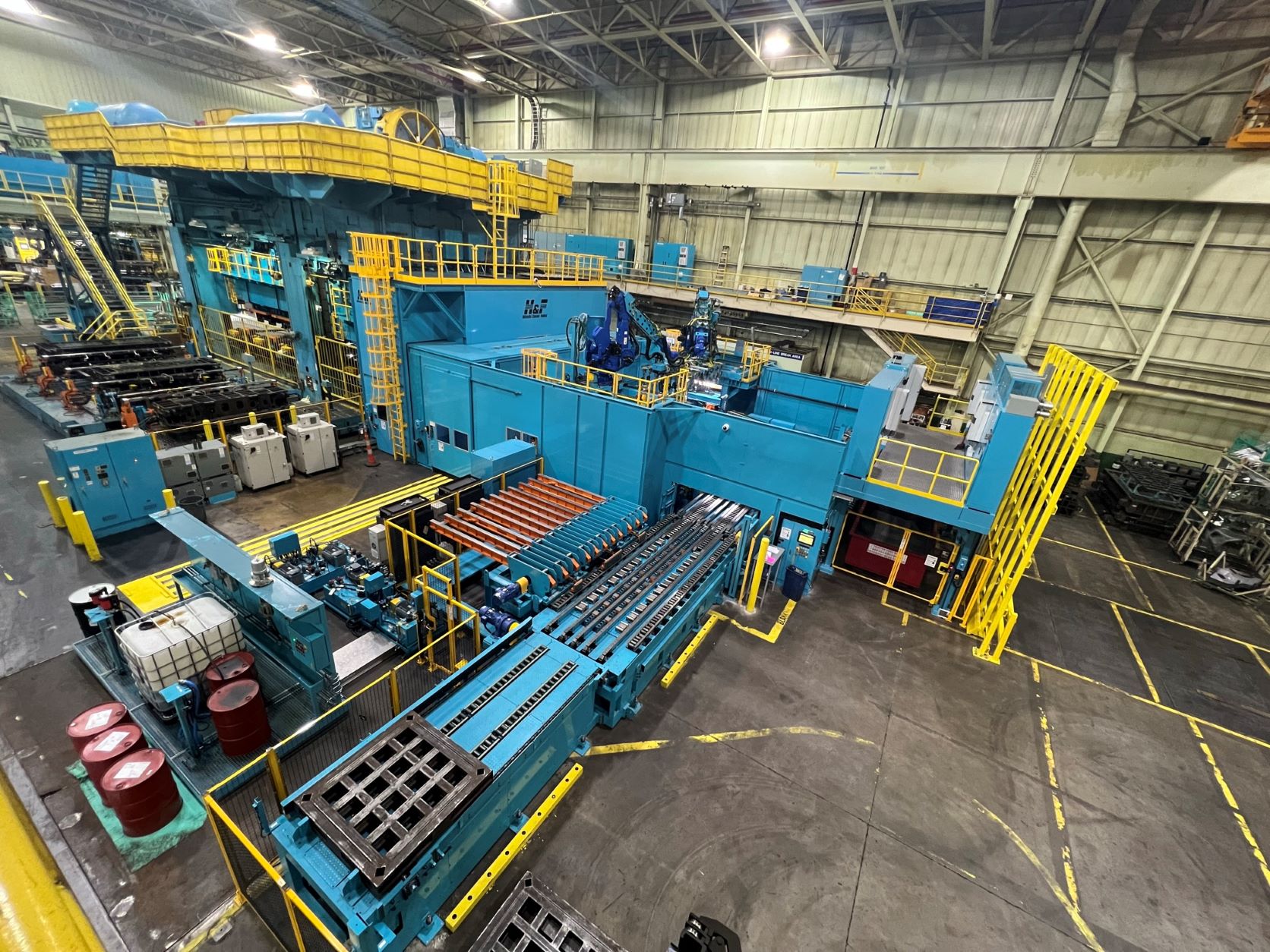
Renewal for the win
Initial planning for the MAP press renewals started in 2017. It takes around two years to complete the required testing for press characteristics such as vibration, position accuracy, and interference.
In addition, the press renewal incorporated completely new technology. Once complete, the press would be capable of stamping the aluminum parts needed for future production of battery electric vehicles (BEVs), take less process time for die changes, and have a faster run rate.
But when project supervisors were called back to Japan in April 2020 due to the COVID-19 pandemic, the team was forced to adapt quickly.
“Our engineering team had to overcome many challenges without the expertise at the spot that we would normally have available,” Zats said. “But it turned into a good learning opportunity for our entire team.”
The project team worked through many hurdles during press install to maintain the production start-up schedule. The lessons they learned will be applied to the next stamping press renewal, which will take place on ELP’s C-line.
The transfer system on the renewed press allows flexibility in die design and faster die maturation during new model startups. In addition, with the ability to stamp aluminum parts, MAP now has two presses—the press installed in 2012 and the newly renewed press—capable of producing stamped parts for BEVs.
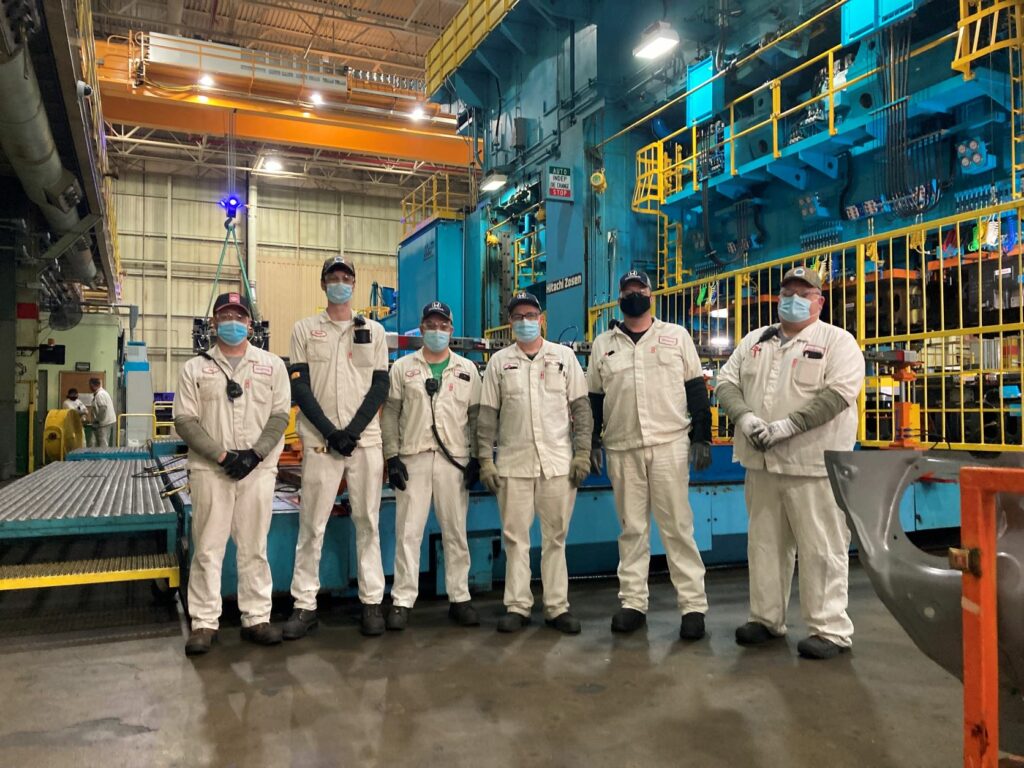