On the brand-new Braze Line, Indiana Auto Plant weldability engineer Samuel Ertel is doing his part to keep vehicle integrity top-notch.
For weldability engineer Samuel Ertel, working at the Indiana Auto Plant (IAP) is all about the braze.
The Laser Braze Line is new to IAP, installed for the 2022 Civic Hatchback. Ertel, a military veteran who worked 20 years for a Honda supplier, was brought into the company to bring the line to life.
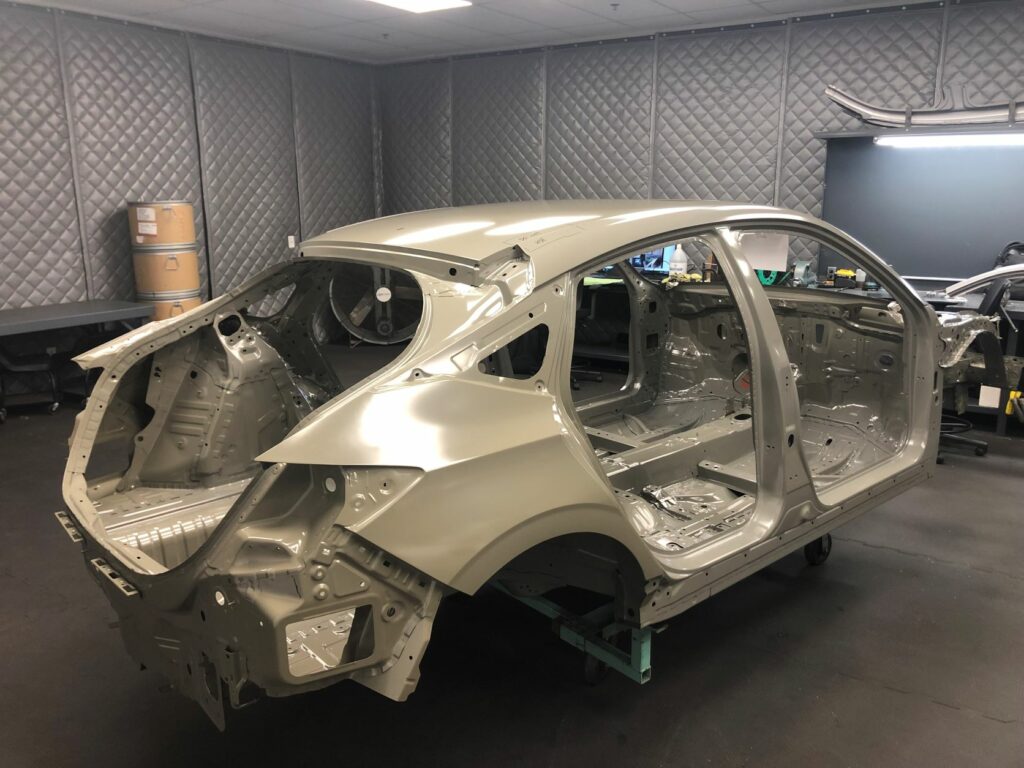
“I got hired in August 2018,” Ertel said. “And it was straight to the process of learning what laser braze even was, and once the core team was developed, we went straight to the installation of the braze line.”
What is laser brazing and what makes the brazing process so unique?
“We are removing the drip-line molding, which is the seam that holds the roof and the side panels together,” Ertel shared. “We take that trim out, bring the roof and side closer together, and fill it with braze wire, which is a completely different material than we’ve used before.”
Nothing like the Braze Line had been done at IAP before, so for the first eight months of his job, Ertel traveled back and forth from Indiana to the Ohio plants that were currently using the process.
“They started it in Ohio. They initiated it. What better place to learn? This couldn’t have happened without the support and guidance from the Ohio team,” he said.
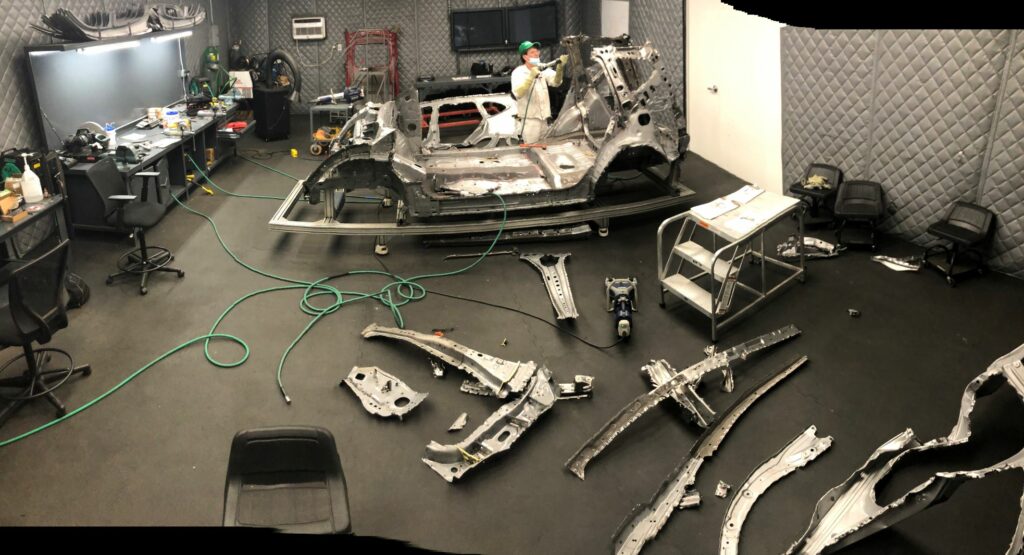
Becoming the strongest
Now the Braze Line line is up and running. Ertel, along with braze team members, starts every shift by validating that the line is operating within the correct parameters in the brand new Braze Line lab.
“We run a small sample through the line, and then we bring it to the lab and put it under a microscope so we can verify that both left and right braze samples meet the dimensional and strength requirements set by Honda,” he said.
That verification process is one of the most important roles a weldability engineer has.
“How the car welds together is one of the factors that impacts how the vehicle will perform in a crash, which is why Honda added an extra layer to the verification process,” Ertel added. “Some other companies may check for visual, aesthetic value. But we have added a structural integrity spec to the braze, which is an actual strength test.”
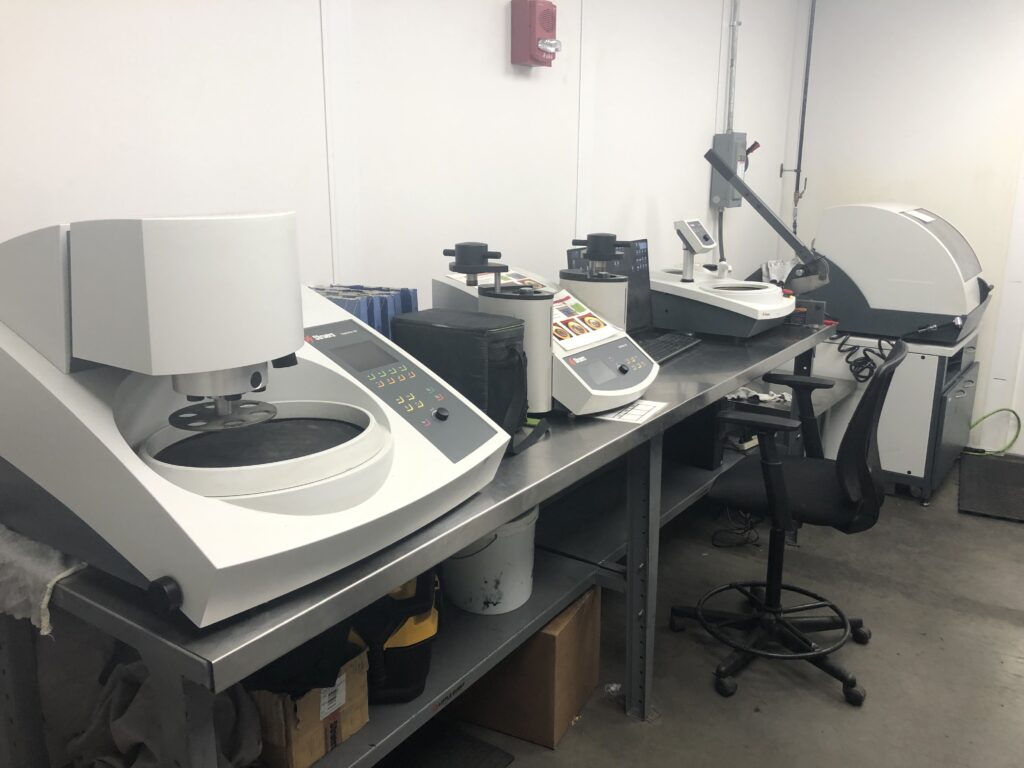
“Destruct” for success
Ertel also runs both new model and annual “destructs” or weld deconstruction, where he and a team take apart a vehicle to verify every spot weld.
“It’s a long process, and it’s a very physically demanding and labor-intensive process,” he said. “But it’s also the best thing to do because you see everything.”
Deconstruction also helps the team determine new best practices and gain a better understanding about how to fix issues when they arise.
“Something the military taught me was attention to detail,” he said. “And that’s critical in not only what we’re doing here, but everything. I can take these pieces to the weld team and show them exactly what the issue is, down to the heat affected zones under the microscope at 50X.”
And that is pivotal.
“At the end of the day, weld integrity is vehicle integrity,” Ertel said.
“With these new spaces, like the lab and the deconstruct room and the new Braze Line itself, we’re able to bring new technologies and levels of quality to IAP,” he added. “The important thing is that we are moving ahead and getting better every day.”
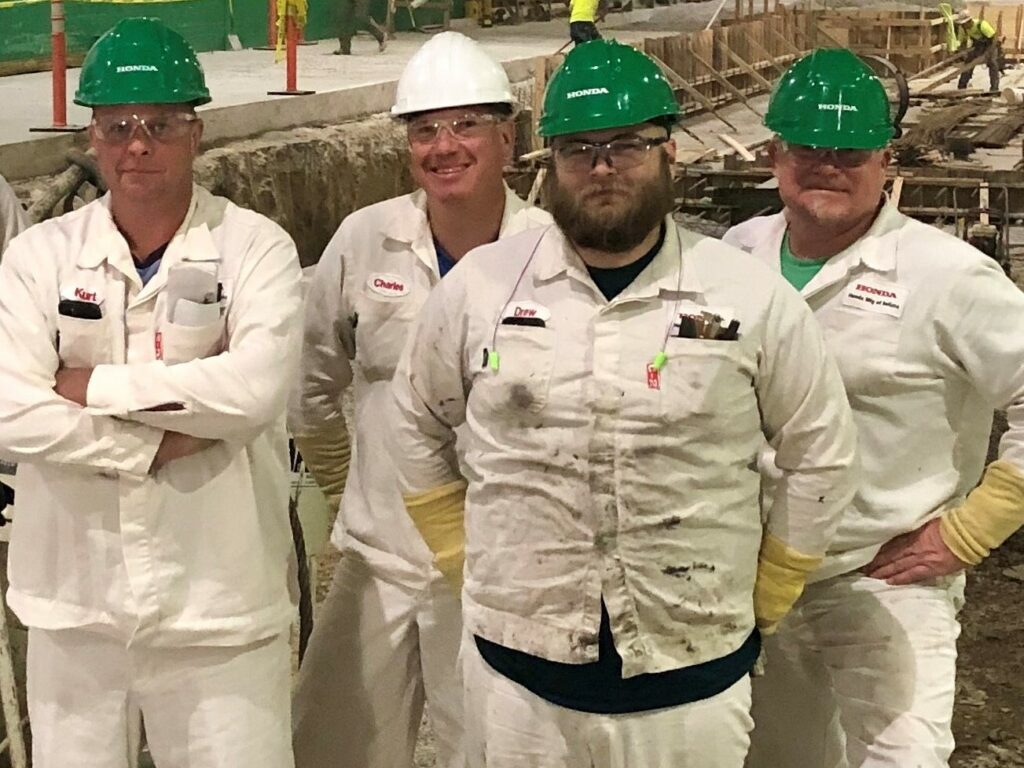